
What is HTC?
Pyrolysis is the treatment of organic matter at elevated temperatures in oxygen-free conditions. This can be done with water (wet pyrolysis) or without water (dry pyrolysis). Wet pyrolysis is called hydrothermal carbonization (HTC), and is the foundation of the C-Green HTC process. HTC was discovered in 1913 by the German chemist Friedrich Bergius. He was awarded the Nobel Prize in 1931 for this discovery.
The C-Green HTC process
An ideal solution for handling wet biowaste such as sewage sludge and bioreactor digestate.
The C-Green HTC process treats sludge in a reactor for one hour at approximately 200 °C. During the process, an aqueous phase forms containing inorganic and organic water-soluble components, along with a slurry phase made up of biocoal particles. As the pressure is reduced, steam is generated. This steam is recycled and injected at the start of the process to preheat the incoming sludge, significantly reducing the need for external energy input.
Water separated from the sludge is sent back to the wastewater treatment plant. If the plant has biogas production, it is possible to increase biogas output using the separated water. Finally, a high-capacity chamber filter press – the same type widely used in the mining and food industries – is employed for efficient dewatering of the HTC slurry, creating a carbon-rich material called HTC biocoal, also referred to as hydrochar.
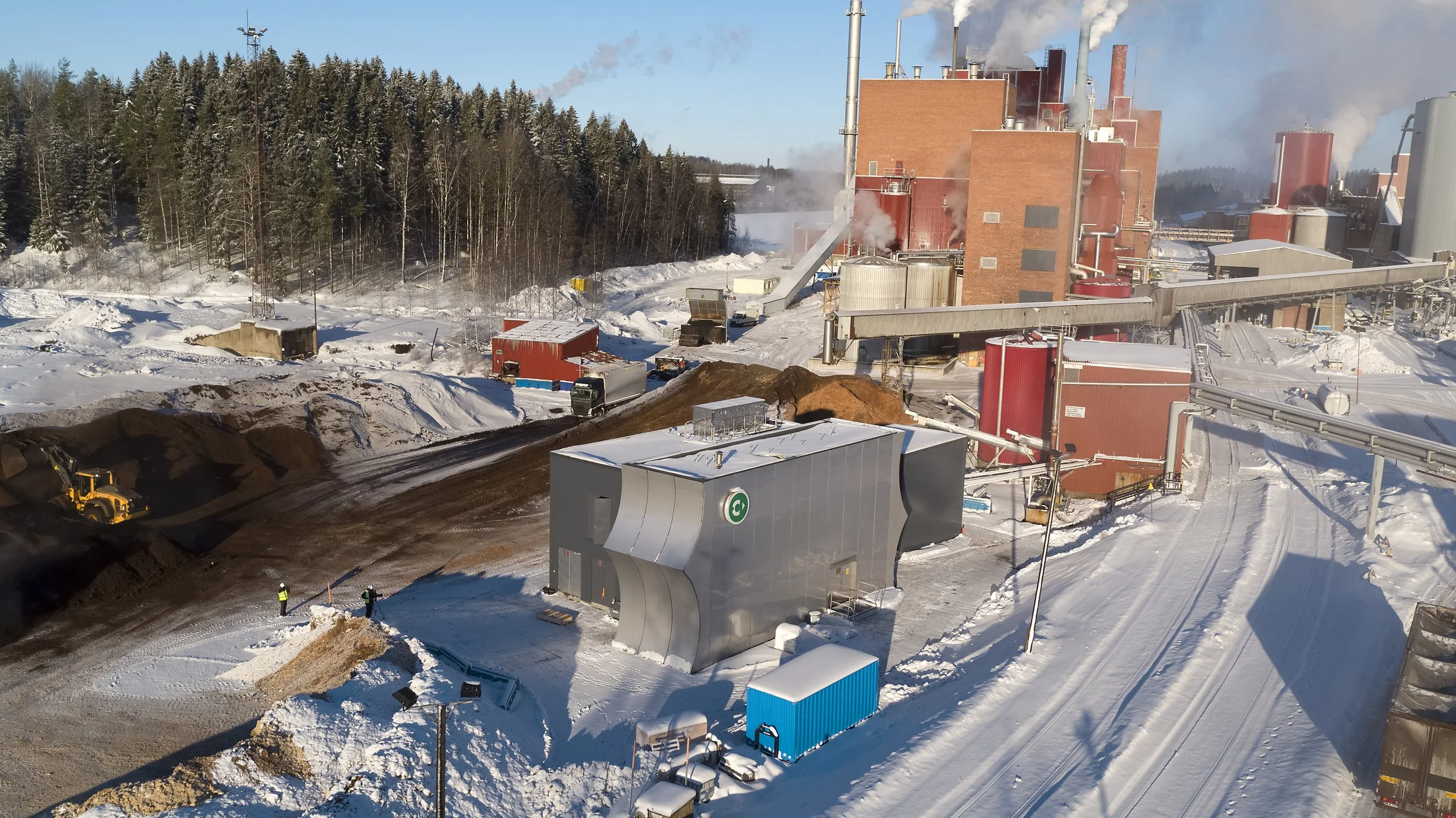
HTC is efficient sludge handling
One C-Green HTC facility has the capacity to process up to 30,000 tons of wet sludge per year — the amount typically produced by a city of 300,000 to 400,000 people.
HTC – for all types of wet biowaste
C-Green's HTC plant is highly flexible and can convert almost any type of wet biowaste — regardless of whether it is digested, non-digested, or has varying moisture content.
   Sewage sludge
   Biogas digestate
   Manure
   Food waste
   Industrial biosludge
   Agricultural residues
   Fiber bank sludge
   Algae and seaweed
